Pellet Machine Dies are key components in biomass pellet machines, which directly determine the quality of pellet molding, production efficiency, and service life of the equipment. As an important tool in the fields of biomass energy, feed processing, and industrial pelletizing, the design and material selection of pellet machine dies play a vital role in the entire production process.
The die holes on the die need to be precisely machined to ensure the uniformity of the size and surface smoothness of the pellets. Pellets for different purposes (such as biomass fuel or feed) may require die designs with different apertures and shapes.
During the pellet production process, the die is in a high pressure, high temperature, and high friction environment for a long time, so it must have extremely high wear resistance. High-quality dies are usually made of special alloy steel or heat-treated steel to extend their service life.
Depending on different application requirements, pellet machine dies can be designed in a variety of specifications and shapes. For example, biomass pellet dies usually have larger apertures, while feed pellet dies require smaller and finer holes.
Modern pellet machine dies can reduce energy consumption and improve production efficiency by optimizing hole layout and surface treatment technology, thereby reducing overall operating costs.
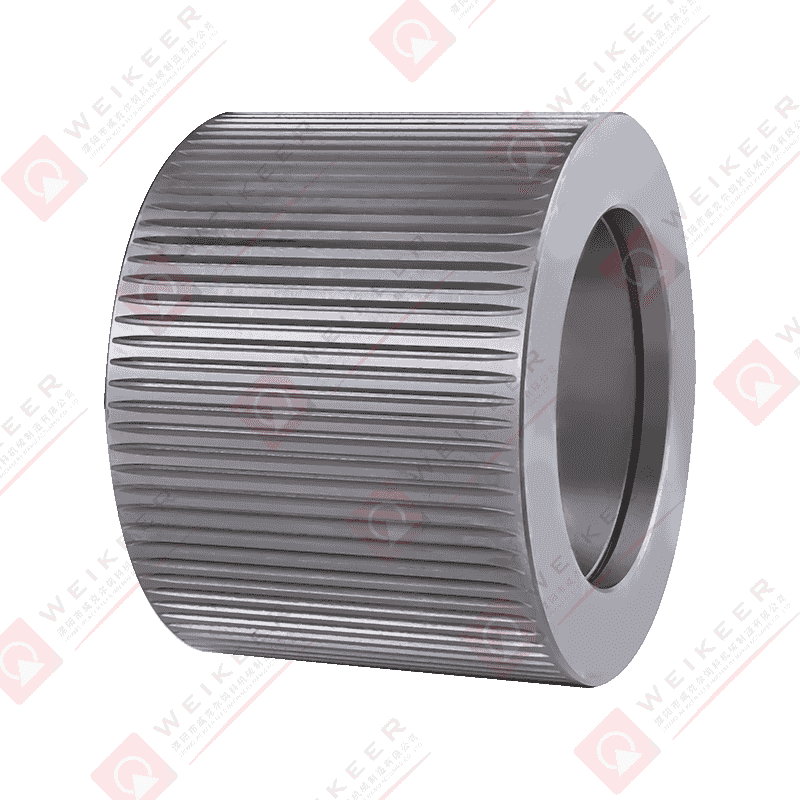
Easy to replace and maintain
Pellet mill dies are usually designed with modular structures, which are easy to replace and repair quickly, reducing downtime.
The working principle of pellet mill dies is based on compression molding technology. When raw materials (such as wood chips, straw, corn flour, etc.) enter the pellet mill, the roller pushes them into the die hole of the die. Under high pressure, the raw materials are compressed and extruded through the die hole to form cylindrical or other shaped pellets. The hole size and shape of the die determine the final specifications of the pellets, while the material and processing accuracy of the mold affect the quality and production efficiency of the pellets.
To ensure efficient production, pellet mill dies need to be cleaned and maintained regularly to prevent the die holes from clogging or excessive wear.
Pellet mill dies are widely used in many industries due to their versatility and reliability:
In biomass pellet production, dies are used to compress raw materials such as wood chips, rice husks, straw, etc. into high-density fuel pellets. These pellets can replace coal and are used in home heating, industrial boilers and power plants.
Feed Processing
Animal feed pellets need to meet specific nutritional ingredients and physical properties, and pellet machine molds can produce feed suitable for different animals (such as chickens, pigs, and cattle) by adjusting the aperture and compression ratio.
Organic Fertilizer
In organic fertilizer production, pellet machine molds are used to compress fermented organic waste into pellets for easy storage, transportation, and application.
Chemical and Pharmaceutical
Pellet machine molds are also used to produce chemical catalysts, tablets, and other industrial pellet products. Their high-precision design can meet strict process requirements.
Future Development Trends
With the global attention to sustainable development and green energy, the research and development direction of pellet machine molds is moving towards the following aspects:
High-performance materials
The application of new alloy steels, ceramic coatings, and nanomaterials will further enhance the wear resistance and corrosion resistance of molds, thereby extending service life and reducing maintenance costs.
Intelligent Design
With the help of computer-aided design (CAD) and finite element analysis (FEA) technology, future pellet machine molds will achieve more optimized hole layout and flow channel design to improve production efficiency and pellet quality.
With the diversification of market demand, pellet machine mold manufacturers will provide more customized options to meet the special needs of different industries and customers.
Green and environmentally friendly manufacturing
The concept of green manufacturing has promoted the development of mold production in a more environmentally friendly direction, such as using recyclable materials or optimizing production processes to reduce carbon emissions.
Automation and intelligent maintenance
Combined with Internet of Things technology, future pellet machine molds will be equipped with sensors to monitor wear in real time and predict replacement time, thereby reducing downtime losses.
As the core component of biomass pellet production, the performance of pellet machine molds directly affects the quality and production efficiency of the product. Whether in the energy, agriculture or industry fields, it has shown irreplaceable value. In the future, with the development of new materials, new technologies and intelligent trends, pellet machine molds will surely play an important role in more high-end application scenarios and contribute to global sustainable development.