Pellet machine dies are one of the most important core components of pellet machine equipment, which directly determines the quality and production efficiency of pellet molding. Whether it is the manufacture of biomass fuel pellets or the processing of animal feed, pellet machine dies play a vital role.
Pellet machine dies need to withstand extremely high pressure and friction, so they are usually made of high-quality alloy steel and undergo heat treatment and surface hardening processes to improve their wear resistance and service life.
High-precision design
The size, shape and distribution of the die holes are precisely calculated to ensure the uniformity and consistency of the pellets. Pellets for different purposes (such as feed pellets or biomass pellets) require different die designs.
Depending on the application requirements, pellet machine dies can be divided into many types, such as flat dies and ring dies. Flat dies are suitable for small equipment, while ring dies are more suitable for large-scale industrial production.
Economical
Although the initial cost of pellet machine dies is high, their long life and high efficiency make them a key component with extremely high cost performance. Reasonable selection and maintenance of molds can significantly reduce production costs.
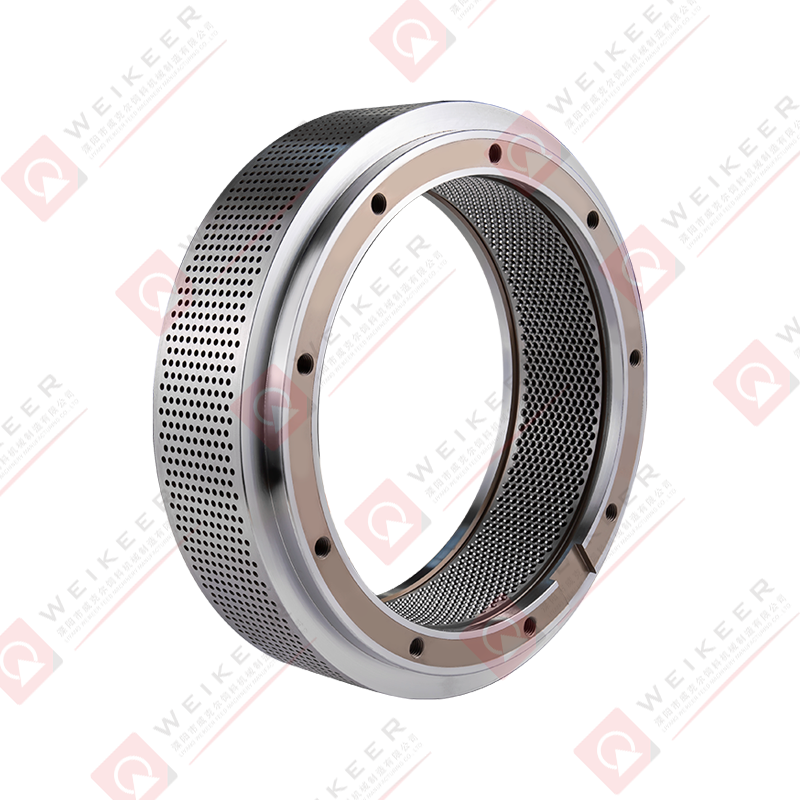
Strong adaptability
Pellet machine molds can adapt to a variety of raw materials, including wood chips, straw, grains, feed, etc., and are widely used in biomass energy, agriculture and animal husbandry.
Working principle of pellet machine molds
The working process of pellet machine molds mainly relies on the effects of high pressure and friction. The following are the key steps of its working principle:
Raw materials enter the mold
After the raw materials (such as wood chips or feed powder) are fed into the pellet machine, they are pushed into the mold hole by a rotating roller or screw.
High-pressure compression
In the mold hole, the raw materials are subjected to great pressure and gradually compressed into a dense particle shape. In this process, the natural adhesives (such as lignin) in the raw materials are activated to play a bonding role.
Pellet extrusion
When the pellets reach a certain density and strength, they are extruded from the other end of the die hole to form regular cylindrical or other shaped pellets.
Cooling and shaping
The extruded pellets further harden during the cooling process and eventually form a stable finished product.
Application fields of pellet machine molds
Biomass energy
In the production of biomass pellet fuel, pellet machine molds are widely used to compress agricultural and forestry wastes such as sawdust, rice husks, and straw into high-density fuel pellets. These pellets have the characteristics of high combustion efficiency and low pollution, and are an ideal choice to replace traditional fossil fuels.
Animal feed processing
The production of animal feed pellets is inseparable from pellet machine molds. By compressing raw materials such as grains, soybean meal, and fish meal into pellets, it can not only improve the nutritional value of the feed, but also reduce waste and facilitate storage and transportation.
Utilization of industrial by-products
Waste generated in industrial production (such as sawdust and papermaking waste) can be processed into pellet fuel or composite materials through pellet machine molds to achieve efficient recycling of resources.
Organic fertilizer manufacturing
Agricultural waste (such as livestock and poultry manure, plant residues) can be processed into organic fertilizer pellets through pellet machine molds, which not only reduces environmental pollution, but also provides high-quality fertilizers for agricultural production.
Food processing
In the production of some special foods (such as pet snacks or instant coffee pellets), pellet machine molds are also used to make products with regular shapes and uniform textures.
Future development trend of pellet machine molds
With the advancement of technology and changes in market demand, pellet machine molds are developing in the following directions:
Research and development of high-performance materials
The application of new alloy materials and surface coating technology will further enhance the wear resistance and corrosion resistance of molds and extend their service life.
Intelligent manufacturing
The introduction of CNC machine tools and 3D printing technology makes the processing of molds more precise, while improving production efficiency and customization capabilities.
Multifunctional design
Future pellet machine molds may integrate more functions, such as adjustable aperture design, to meet the needs of different raw materials and particle specifications.
Green and environmental protection
The research and development of environmentally friendly molds will become a trend, such as using recyclable materials to manufacture molds to reduce resource consumption and environmental impact.
As the core component of pellet forming equipment, the performance and quality of pellet machine molds directly affect the quality and production efficiency of pellet products. Whether in biomass energy, feed processing or other fields, pellet machine molds have shown irreplaceable value. In the future, with the continuous innovation of technology and the growth of market demand, pellet machine molds will surely play a greater role in more fields and contribute to the sustainable development of human society.