In the field of pellet production, pellet machine dies are key components that determine product quality and production efficiency. Whether in feed processing, wood pellet production or biomass energy, pellet machine dies play a vital role. By extruding raw materials into pellets of the desired shape under high pressure, dies help improve production efficiency and ensure the uniformity and density of pellets.
Pellet machine dies are the core component of pellet production equipment. Its basic working principle is to extrude raw materials (such as feed, wood chips, biomass, etc.) through the holes of the die under high temperature and high pressure. When the raw materials enter the pellet machine, multiple small holes in the die will compress and shape these raw materials to form pellets. The rollers of the pellet machine work closely with the die to provide sufficient pressure to ensure that the raw materials are completely extruded into uniform pellets.
The design of the die directly affects the quality and production speed of the pellets. The hole diameter, hole shape and hole spacing of the die will have an important impact on the final quality of the pellets.
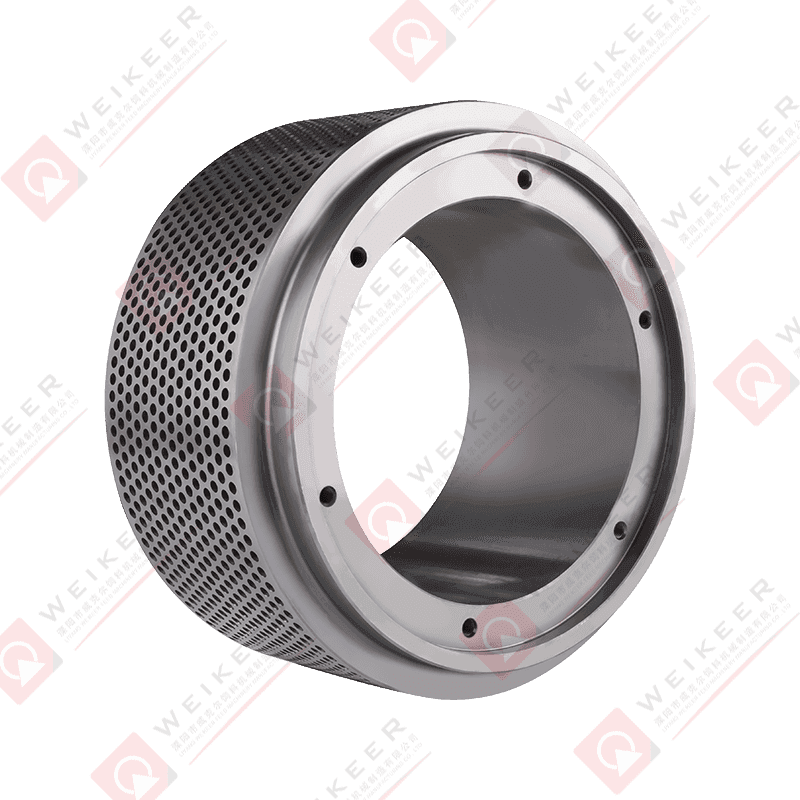
Pellet machine dies are usually made of high-strength alloy steel, chrome steel or other wear-resistant materials, which makes them have a long service life. Wear resistance is particularly important when processing hard raw materials (such as wood chips, straw, etc.). Highly wear-resistant molds can reduce maintenance costs and improve production efficiency.
The aperture and hole shape of the pellet machine mold can be customized according to different production needs. For example, in feed production, smaller pellets are usually required, while in wood pellet production, larger pellets may be required. By adjusting the aperture and hole shape of the mold, producers can produce a variety of different types of pellets.
The design of the pellet machine mold not only affects the shape of the pellets, but also directly affects the uniformity and density of the pellets. The size of the mold aperture, the arrangement of the holes, and the smoothness of the inner wall all affect the density and uniformity of the pellets. High-quality molds ensure the consistency of each pellet, thereby improving the quality and operability of the product.
The design of the pellet machine mold makes it relatively easy to replace and maintain. By regularly checking and replacing the mold, the manufacturer can ensure the long-term stable operation of the pellet production line. The maintenance cycle and replacement time of the mold depend on the production conditions and the raw materials used.
In the feed industry, pellet machine molds are widely used in the production of animal feed. Different animals (such as pigs, cattle, chickens, etc.) require different feed pellet sizes and hardness, so the aperture design of the mold also needs to be adjusted according to the needs. The excellent performance of the mold can improve the digestibility and nutritional value of the feed.
With the continuous development of renewable energy, the production of biomass pellets (such as wood chip pellets, straw pellets, etc.) has gradually become an important source of energy. Pellet machine molds play a vital role in biomass pellet production. They help compress various biomass raw materials into compact pellets, which can be used as fuel, which is both energy-saving and environmentally friendly.
Wood pellet production is one of the important applications of pellet machine molds. The mold design needs to ensure that sawdust and other wood raw materials are fully compacted under high temperature and high pressure to form compact pellets. These pellets can not only be used as fuel, but also in fields such as gardening and soil improvement.
In fertilizer production, pellet machine molds are used to compress various chemical raw materials into pellets for easy transportation, storage and use. The characteristics of pellet fertilizers are uniform particles, easy application, and help improve the growth effect of crops.
Different raw materials require different types of molds. For example, hard materials such as wood chips and straw require molds with higher wear resistance, while feed production requires finer apertures.
According to the particle size and density requirements of the final product, select a mold with appropriate aperture and hole shape. The uniformity and hardness of the particles are important indicators for evaluating the quality of the mold.
The material determines the durability and service life of the mold. High-quality alloy steel or chrome steel materials can extend the service life of the mold and reduce the failure rate.
The aperture and hole shape design of the mold will affect the production efficiency. Proper design can improve the overall operating efficiency of the production line and reduce energy consumption.
The pellet machine mold is an indispensable key component in the pellet production process, which directly affects the quality of the pellets, production efficiency and service life of the equipment. By selecting the right mold, producers can improve the uniformity, density and hardness of the pellets and ensure high-quality output of the product. With the advancement of technology, the design of pellet machine molds is also constantly optimized to meet the needs of different application fields. Whether in feed processing, wood pellet production or biomass energy, pellet machine molds play an important role and contribute to green energy and efficient production.