Animal Feed Pellet Die is a key component in the feed pellet machine, which directly affects the molding quality, production efficiency and equipment life of feed pellets. As an important tool in modern animal husbandry and feed industry, animal feed pellet die not only determines the shape and density of feed pellets, but also has an important impact on the nutritional value of feed and the palatability of animals.
The design and manufacturing process of the die are directly related to the quality and production efficiency of feed pellets, so it is an indispensable core component in feed processing equipment.
The working process of animal feed pellet die can be divided into the following steps:
Raw material pretreatment
Before entering the die, feed raw materials usually need to be crushed, mixed and tempered to ensure that they have appropriate moisture and viscosity for easy molding.
Extrusion molding
The pellet machine presses the raw materials into the small holes of the die through rotating rollers to form dense pellets under high pressure. The size and shape of the die aperture determine the final specifications of the pellets.
Cutting and cooling
The formed pellets are extruded from the other side of the die and cut into the required length by the cutting device. Subsequently, the pellets are cooled and dried to further improve their hardness and stability.
To meet the requirements of high strength, wear resistance and corrosion resistance, animal feed pellet molds are usually made of the following high-quality materials:
Alloy steel Alloy steel molds are the most common choice, with high hardness and wear resistance, suitable for processing ordinary feed pellets.
Stainless steel Stainless steel molds are suitable for producing high-humidity or highly corrosive feed (such as aquatic feed), which can effectively resist corrosion and extend service life.
Tungsten carbide coated molds Tungsten carbide coated molds add a layer of superhard coating on the mold surface through a special process, which significantly improves wear resistance and is suitable for large-scale continuous production.
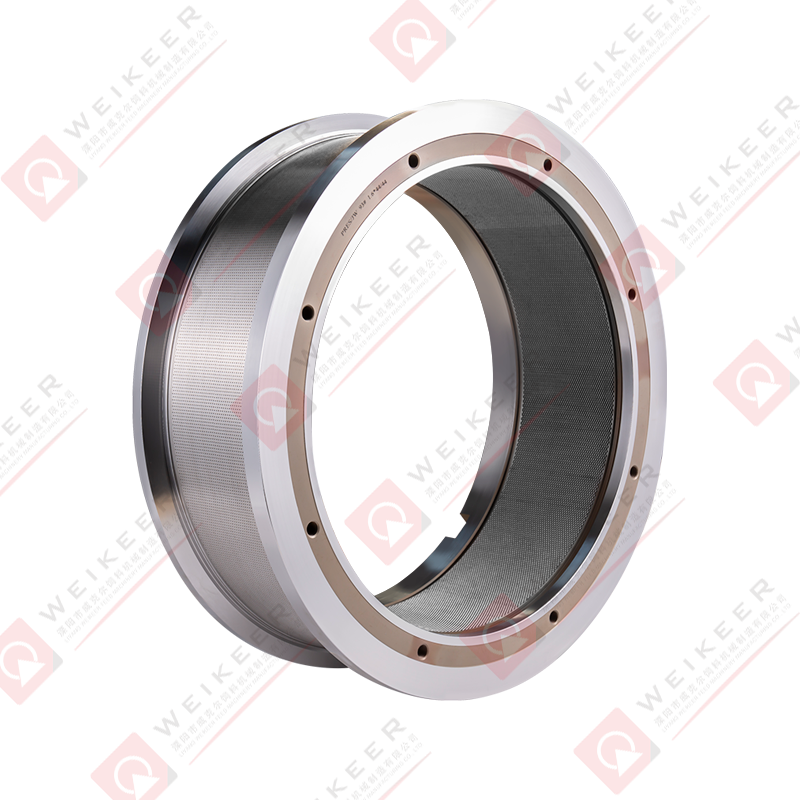
Bimetallic molds Bimetallic molds combine high-strength substrates and wear-resistant surface layers, which not only ensures the overall strength of the mold but also improves its service life.
Poultry feed production Poultry feed pellet molds are usually designed with a smaller aperture to produce delicate and easily digestible pellets suitable for poultry such as chickens and ducks.
Pig feed production Pig feed pellet molds need to take into account the hardness and palatability of the pellets, and are often used to produce medium-sized pellets to meet the needs of pigs at different growth stages.
Cattle and sheep feed production
Cattle and sheep feed pellet molds are designed with larger pores to produce pellets with higher crude fiber content, which is helpful for digestion and absorption by ruminants.
Aquatic feed production
Aquatic feed pellet molds need to have good corrosion resistance and produce floating or sinking pellets to adapt to the feeding habits of fish and other aquatic animals.
Pet feed production
Pet feed pellet molds focus on the appearance and taste of pellets and are often used to produce pellets with various shapes and bright colors to attract the attention of pet owners.
Improve production efficiency
High-quality molds can significantly increase the production capacity of feed pellet machines and reduce downtime and maintenance costs.
Optimize feed quality
The design of the mold directly affects the density, hardness and uniformity of feed pellets, thereby improving the nutritional value of feed and the feeding effect of animals.
Extend equipment life
High-quality mold materials and precise manufacturing processes can effectively resist wear and extend the service life of molds and pellet machines.
Strong flexibility
Different types of molds can be customized according to customer needs to meet the production needs of various feed pellets.
With the continuous development of the feed industry and the advancement of technology, animal feed pellet molds are developing in the following directions:
Intelligent design
Use computer simulation and 3D printing technology to optimize mold design and improve pellet molding quality and production efficiency.
New material research and development
Develop new materials that are more wear-resistant and corrosion-resistant to further improve the service life and performance of molds.
Environmental protection and sustainability
Promote the use of recyclable materials to manufacture molds, and optimize production processes to reduce resource waste and environmental pollution.
Multifunctional integration
Develop universal molds that can adapt to a variety of feed types and pellet specifications to reduce the equipment investment cost of enterprises.
As the core component in feed production, animal feed pellet molds are not only a guarantee of efficient production, but also the key to feed quality. Whether it is poultry, livestock or aquaculture, it is silently supporting the development of modern animal husbandry. In the future, with the continuous emergence of new materials and new technologies, animal feed pellet molds will continue to innovate, provide more efficient and reliable solutions for the feed industry, and also contribute to global food security and sustainable development.