The wear resistance of pellet mill screw type stainless steel dies plays a pivotal role in the overall efficiency, consistency, and longevity of pellet production. Understanding the implications of die wear and how it impacts the pelletizing process is crucial for manufacturers aiming to optimize their production lines and maintain high-quality output.
The Role of Stainless Steel Dies in Pellet Production
Pellet mills are at the core of many industries, including agriculture, biomass energy, and animal feed manufacturing. The screw-type stainless steel die is a critical component in these mills, responsible for compressing raw material into uniform pellets. This die undergoes continuous pressure, abrasion, and thermal stress, which makes its wear resistance a key factor in the production process. The higher the wear resistance of the die, the better the pellet quality, production capacity, and equipment lifespan.
Wear Resistance and Its Direct Impact on Pellet Quality
Wear resistance refers to the ability of the stainless steel die to withstand the constant friction and stress it encounters during pellet production. Over time, dies inevitably experience some form of wear, which can lead to irregularities in pellet size, shape, and density. These inconsistencies are detrimental to the end product, especially when precision and uniformity are required. A worn die may lead to the production of pellets with uneven sizes or poor compression, which can reduce the quality of the final product and affect its performance in its intended application.
In industries such as animal feed manufacturing, the nutritional value of pellets can be compromised if the die does not compress the raw materials evenly. This irregularity may lead to substandard feed, which can adversely affect livestock health and growth. Similarly, in biomass pellet production, inconsistent pellet quality can result in reduced combustion efficiency, affecting energy output and increasing operational costs.
Increased Production Efficiency
Wear resistance has a direct bearing on the efficiency of the pelletizing process. As the die wears down, the efficiency of the pellet mill decreases, leading to more frequent maintenance, longer downtimes, and increased material wastage. Dies with superior wear resistance ensure more consistent and continuous operation, allowing for higher production rates and reduced maintenance costs. The ability to maintain optimal performance for longer periods without frequent replacements or repairs can significantly reduce overall operating costs, making the production process more economically viable.
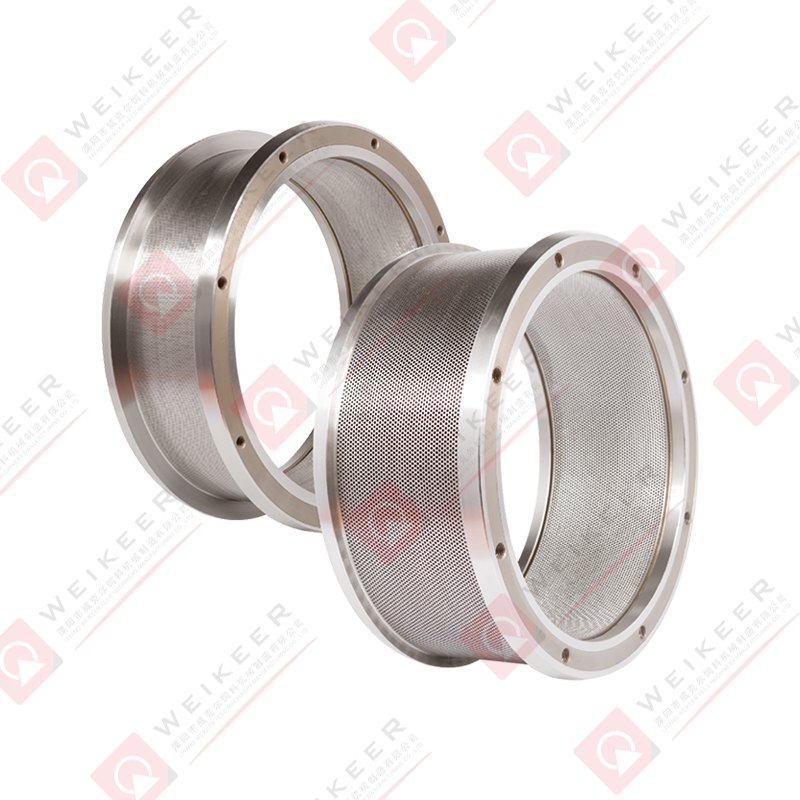
Furthermore, with increased wear resistance, the risk of mechanical failures is minimized. This results in fewer unplanned downtimes, helping manufacturers maintain production schedules and meet customer demands without delays.
Prolonged Equipment Lifespan
A high-quality, wear-resistant stainless steel die extends the overall lifespan of the pellet mill, offering a return on investment that justifies the upfront costs. Stainless steel, when engineered with high wear resistance, can withstand repeated mechanical stress and environmental conditions without significant degradation. This durability ensures that the pellet mill operates smoothly for longer, which is crucial in industries where uninterrupted production is essential.
Additionally, a longer-lasting die reduces the need for frequent replacements and repairs, saving both time and money. Manufacturers can allocate resources to other aspects of their operations, focusing on enhancing their product offerings or expanding capacity.
Cost Implications of Poor Wear Resistance
The cost implications of poor wear resistance are far-reaching. Not only does it affect the quality of the final product, but it also leads to significant operational inefficiencies. Frequent die replacements, more complex repairs, and prolonged downtimes all contribute to a rise in production costs. Moreover, if the pellet quality suffers due to die wear, manufacturers may face reputational damage and a loss of customer trust.
Poor wear resistance also impacts the overall energy consumption of the pellet mill. As the die wears down, it may require higher levels of energy to compress the material, reducing the energy efficiency of the process. This results in higher energy bills and a larger environmental footprint.
The wear resistance of the pellet mill screw type stainless steel die is a crucial factor that directly impacts the quality, efficiency, and cost-effectiveness of pellet production. By investing in high-quality, wear-resistant dies, manufacturers can ensure consistent product quality, minimize downtime, reduce maintenance costs, and prolong the lifespan of their equipment. Given the significant role these dies play in the overall production process, it is essential for manufacturers to prioritize wear resistance when selecting pellet mill components. This investment ultimately translates into improved operational efficiency and a stronger competitive edge in the marketplace.