The design of a pellet mill screw type stainless steel die is crucial to enhancing the efficiency and quality of the pelletizing process. A well-crafted die can significantly influence the performance of the pellet mill, improving throughput, energy consumption, and the overall quality of the pellets. To optimize the pelletizing process, several key factors must be considered during the design of the screw type stainless steel die.
Understanding the Role of the Die in Pelletizing
The pelletizing process involves compressing raw materials into uniform pellets, typically using heat and pressure. The die plays a central role in this process, as it is responsible for shaping the material and ensuring the correct density and size of the pellets. The screw-type die, in particular, offers superior control over material flow and is commonly used in a variety of industries, including feed, biofuels, and pharmaceuticals.
The die’s function is not simply to shape the pellets but to provide the necessary compression and friction for the raw materials to bind together. This makes the design of the die integral to achieving optimal pellet quality. When designing a screw type stainless steel die, several factors must be taken into account to ensure that it performs at its peak.
Material Selection: Stainless Steel and Its Advantages
The choice of material for the die is a foundational step in the design process. Stainless steel, particularly high-grade alloys, is often the material of choice due to its durability, resistance to wear, and corrosion resistance. Given the high pressure and temperature conditions during pelletizing, using stainless steel ensures longevity and minimizes maintenance costs.
Stainless steel’s resistance to corrosion is crucial, especially when processing moist or abrasive materials. Furthermore, its inherent strength allows the die to withstand the pressures exerted during the pelletizing process, which is vital for maintaining consistent pellet quality over time.
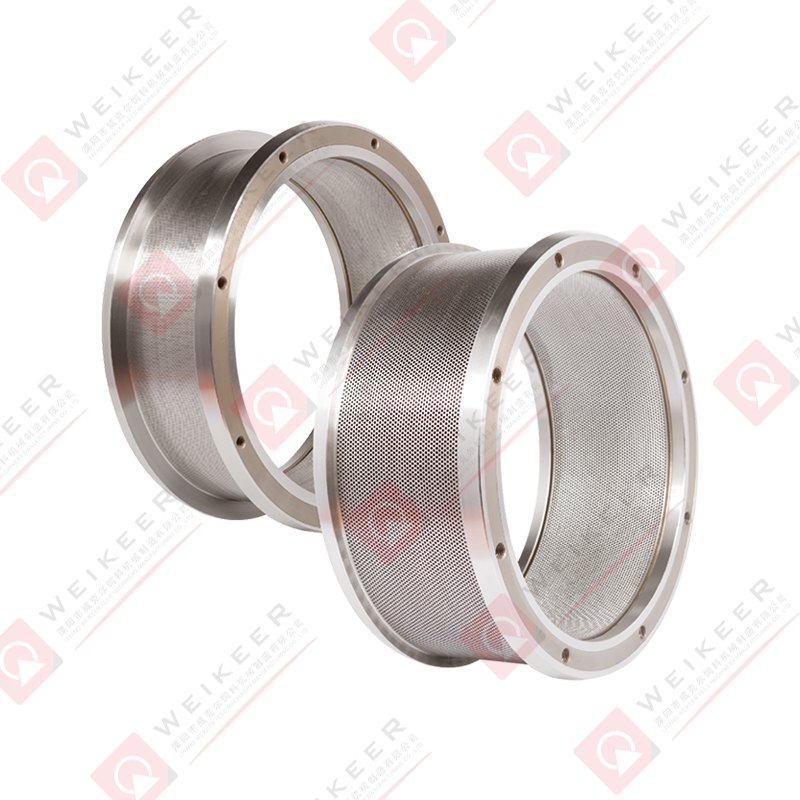
Die Design: Ensuring Optimal Flow and Compression
One of the most critical aspects of die design is ensuring optimal material flow. The screw type die must facilitate an even and controlled flow of the raw material to prevent clogs or inconsistent pellet sizes. The screw and die should be carefully engineered to ensure that the raw material moves smoothly through the die channels and is compressed uniformly.
The die’s diameter, length, and the number of holes or apertures it contains all play a significant role in the flow characteristics. A larger diameter can allow for a higher throughput, but it may also increase the risk of material segregation and lower pellet density. Smaller dies provide greater compression, resulting in more uniform pellets but can limit the production capacity.
To optimize the die’s performance, it’s essential to tailor its design to the specific material being processed. For example, denser or more fibrous materials may require a die with tighter holes and a higher compression ratio, while less dense materials may perform better with a larger aperture die. The number and pattern of the holes or openings can also influence the pellet's texture, strength, and appearance, making it important to design these features according to the desired output specifications.
Cooling and Lubrication Mechanisms
To optimize the pelletizing process, it is essential to incorporate effective cooling and lubrication systems. Cooling prevents excessive heat buildup, which can degrade the material and cause the die to wear prematurely. A well-designed die will have efficient cooling channels to dissipate heat evenly during operation, ensuring that the pellets maintain their integrity and consistency.
Lubrication also plays a key role in maintaining die performance. Proper lubrication reduces friction and wear on the die, preventing material build-up and ensuring smooth operation. In pellet mills, lubrication systems are often automated to ensure continuous application, reducing the need for manual intervention and improving overall efficiency.
Surface Treatment and Finishing
The surface finish of the die is another important consideration for optimization. A smooth, well-polished surface reduces the likelihood of material sticking to the die, ensuring consistent pellet output and easy maintenance. Additionally, surface treatments such as coating the die with wear-resistant materials can prolong its life and improve overall efficiency. These treatments reduce wear and tear on the die, allowing it to maintain its performance for longer periods, which is essential for reducing downtime and enhancing productivity.
Precision and Tolerances
High precision in the design and manufacturing of the die is critical for ensuring that the pellets are of uniform size and density. Tight tolerances are required to maintain consistency throughout the pelletizing process. Even slight variations in die dimensions can lead to uneven pellet production, leading to product quality issues or machine inefficiency.
The screw type die should be manufactured with tight tolerances and precise alignment to ensure that the material is uniformly compressed as it moves through the die. This precision also contributes to maintaining the desired throughput and prevents material wastage, making the entire pelletizing process more cost-effective.
Designing a screw type stainless steel die to optimize the pelletizing process involves a careful balance of material selection, die geometry, compression mechanisms, cooling and lubrication systems, surface treatments, and manufacturing precision. By considering all these factors and tailoring the design to the specific requirements of the material being processed, manufacturers can enhance the performance and durability of their pellet mills. A well-designed die can result in higher throughput, reduced wear, improved pellet quality, and, ultimately, a more efficient pelletizing process.