When producing high-quality biomass pellets, moisture control is a pivotal factor that directly influences the efficiency of the pelletizing process and the final product's performance. The Pellet ring die of biomass pellets plays a vital role in this aspect, acting as a crucial component in regulating the moisture content of the biomass feedstock during the pressing process. Its design, material, and operational parameters contribute not only to pellet quality but also to the energy efficiency and longevity of the equipment. Understanding how the pellet ring die impacts moisture management is essential for any pellet producer looking to optimize their operations.
The pressing process in pellet production involves transforming raw biomass, often with varying moisture levels, into uniform pellets. In this stage, excess moisture needs to be properly managed to prevent pellet degradation and ensure optimal combustion efficiency. Too much moisture in the biomass can result in poor pellet formation, causing issues like weak, brittle pellets or increased energy consumption during the drying phase. On the other hand, insufficient moisture can lead to excessive friction and wear on the pellet ring die, as well as incomplete pellet formation. This is where the design of the pellet ring die becomes crucial.
The hole design and size of the die directly affect how the moisture in the biomass is handled during the compression process. As the material is forced through the die, the pressure applied causes moisture to evaporate and exit the biomass. The precise control of pressure within the die ensures that the moisture content is balanced to achieve a uniform pellet size and density, which is essential for high combustion efficiency. If the moisture content is too high or too low during this stage, the die may struggle to produce uniform pellets, affecting both the quality of the product and the operational efficiency. In this sense, the die does more than just shape the pellets—it actively influences the moisture balance throughout the process.
Moreover, the material used for the pellet ring die, often stainless steel, contributes to the moisture control capabilities. Stainless steel’s resistance to corrosion and wear ensures that the die maintains consistent pressure and performance over time, even when processing moist or wet biomass materials. The smooth surface of the die helps minimize friction, which in turn reduces the chances of moisture being trapped within the die or escaping unevenly. The smoothness of the die also contributes to more efficient heat transfer, which is vital in maintaining the right temperature and moisture levels for optimal pellet formation.
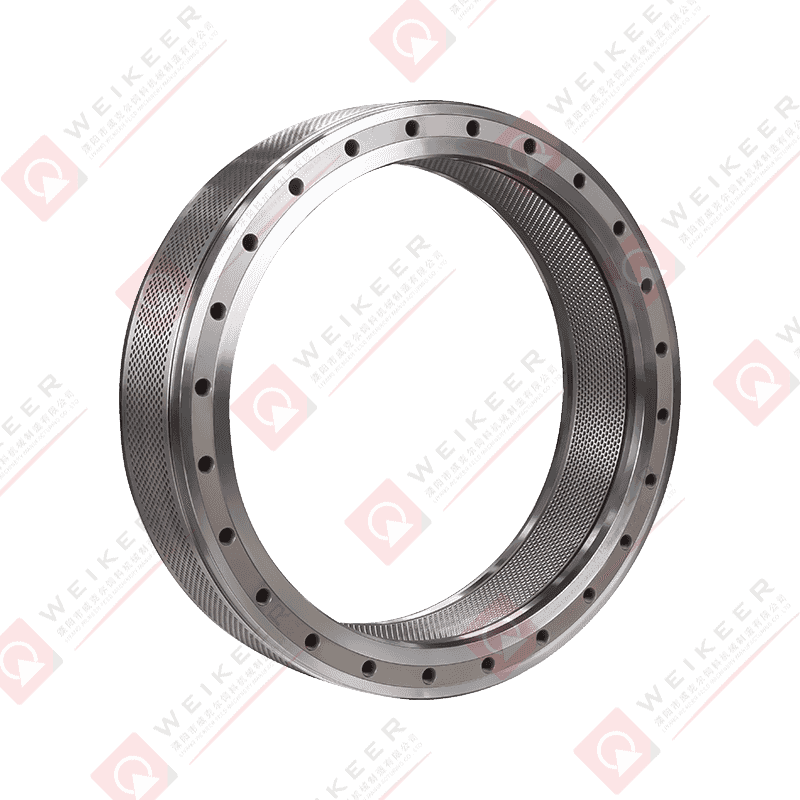
While the pellet ring die is integral to controlling moisture during the pressing phase, it also works in conjunction with other components, such as the screw feeder and the pelletizing machine, which further help regulate the moisture content. The screw feeder, for instance, ensures that biomass is fed consistently into the die, while the pelletizing machine applies the right amount of pressure. Together, these elements create the ideal environment for moisture content optimization, ensuring that the pellets are neither too dry nor too wet. This balance is essential not only for pellet quality but also for maintaining the energy efficiency of the overall production process.
The pellet ring die is far more than just a shaping tool—it’s an essential component that significantly influences moisture control during biomass pellet production. By understanding how the design and material of the die work in harmony with the rest of the pelletizing equipment, manufacturers can ensure that moisture levels are carefully managed, resulting in high-quality pellets with optimal combustion efficiency, density, and durability. When used correctly, the pellet ring die helps maintain the delicate balance of moisture, contributing to the overall efficiency of the pellet production process and meeting the growing demand for sustainable and high-performing biomass pellets.