In modern aquaculture, high-quality feed is the key to ensure the healthy growth of aquatic animals such as fish and shrimp. The Aquatic Feed Pellet Mill is the core equipment for producing high-quality feed. Its core component, the Ring Die, determines the molding quality, production efficiency and service life of the feed pellets.
Forming Feed Pellet
The Ring Die is the core tool for forming feed pellets. Through the small holes of the Ring Die, the raw materials are squeezed into pellets of specific shapes and sizes to meet the feeding needs of different aquatic animals.
Controlling Pellet Quality
The aperture, hole depth and surface finish of the Ring Die determine the hardness, density and appearance quality of the feed pellets. For example, a smaller aperture is suitable for producing small pellet feed for young fish or shrimp fry, while a larger aperture is suitable for adult fish.
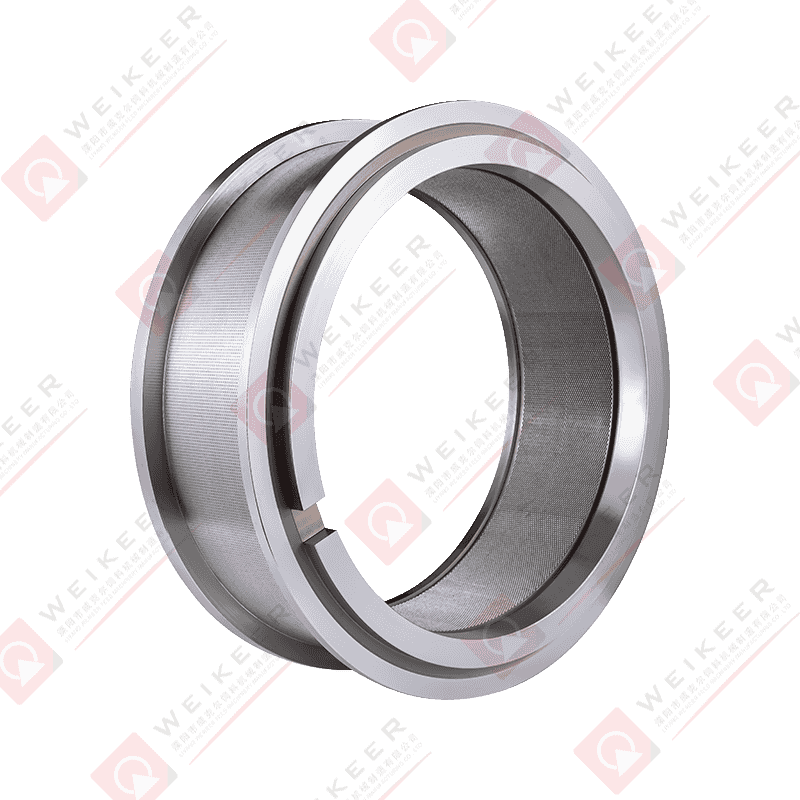
Improve Production Efficiency
High-quality ring dies can withstand high-intensity working pressure and maintain long-term stable performance, thereby improving the production efficiency of the equipment and reducing downtime for maintenance.
Extending Equipment Life
The quality of the Ring Die directly affects the operating status of the pellet machine. High-quality ring dies can reduce wear and reduce energy consumption, thereby extending the service life of the entire machine.
Design features of ring dies
Material selection
Ring dies are usually made of high-strength alloy steels, such as chrome-molybdenum steel or stainless steel. These materials have excellent wear resistance and corrosion resistance and can adapt to long-term high-pressure working environments.
Hole design
The hole design of the ring die varies depending on the feed type and purpose. Common hole types include straight hole type, stepped hole type and tapered hole type. Different hole types affect the compression ratio, density and molding effect of feed particles.
Surface treatment
The inner surface of the ring die is precision machined and polished to reduce friction, improve the smoothness of the raw material when passing through, and extend the service life.
Cooling and lubrication
During high-speed operation, the ring die generates a lot of heat. Therefore, many modern ring dies are designed with built-in cooling channels or adopt external lubrication systems to prevent deformation or damage caused by overheating.
Ring die manufacturing process
Material forging and heat treatment
The manufacturing of ring dies starts with the forging of high-quality steel, followed by strict heat treatment processes (such as quenching and tempering) to enhance its hardness and wear resistance.
Precision drilling
The ring die is drilled using high-precision CNC machine tools to ensure that the size, depth and position of each small hole are exactly the same. This is a key step to ensure the quality of feed pellets.
Surface hardening
To further improve wear resistance, the inner surface of the ring die is carburized or nitrided to give it higher hardness and wear resistance.
Quality inspection
The finished ring die is subject to strict quality inspection, including hardness testing, aperture measurement and surface finish inspection to ensure that it meets the design standards.
Application areas of ring dies
Fish feed production
Different types of fish require feed pellets of different specifications. For example, small fish (such as tilapia) require fine pellets, while adult carp require larger and harder pellets. The design of the ring die can be flexibly adjusted according to demand.
Shrimp feed production
Shrimp feed usually requires smaller and finer particles, while having high stability in water. The hole shape and compression ratio design of the ring die are crucial for this.
Special aquatic feed
For high-end aquaculture (such as eel, sturgeon, etc.), the ring die needs to meet higher standards of feed molding requirements to ensure uniform distribution of nutrients and palatability of particles.
Experimental and customized feed
In the field of scientific research, researchers often need to produce specially formulated feed. The flexibility of the ring die enables the pellet machine to quickly adapt to different experimental needs.
Market trends and development prospects
With the rapid development of the global aquaculture industry, the demand for high-quality feed is increasing, and ring die technology is also constantly improving. Here are a few trends worth paying attention to:
Intelligent manufacturing
Modern ring die manufacturing is increasingly using intelligent equipment and big data analysis technology to improve production accuracy and efficiency.
Environmental protection and sustainability
The research and development of new ring die materials is moving towards a more environmentally friendly direction, such as using recyclable alloys or low-energy production processes to reduce resource waste.
Multifunctional design
In the future, ring molds will pay more attention to versatility, adapt to a variety of feed types and production conditions, and meet diverse market needs.
Global expansion
In emerging markets such as Asia, Africa and South America, the rapid growth of the aquaculture industry will drive the demand for ring molds and related equipment.
As the core component of feed production, the ring mold of aquatic feed pellet machine plays an irreplaceable role in improving feed quality and production efficiency. From material selection to precision manufacturing, every link reflects the progress of technology and innovation of the industry. In the future, with the continuous expansion of the aquaculture industry and the continuous upgrading of technology, ring molds will continue to promote the efficiency and refinement of feed production, and contribute to global food safety and sustainable development. Ring molds are not only the heart of aquatic feed pellet machines, but also the cornerstone of the development of modern aquaculture.