Pellet mill dies are the core components of pellet mill equipment. They directly affect the quality and production efficiency of products such as pellet feed, wood chip pellets, and biomass fuel pellets. Whether in agriculture, animal husbandry or new energy industries, pellet mill dies play a vital role. This article will introduce in detail the types, working principles, manufacturing materials, influencing factors, and how to choose the right die to help companies optimize production efficiency and improve product quality.
1. Function of pellet mill dies
The main function of a pellet mill die is to squeeze powdered or finely crushed raw materials into uniform-sized pellets. During the production process, the raw materials are forced through the holes on the die under pressure to form pellets of a specific diameter and length. This process involves high temperature and high pressure, so the durability and precision of the die have a direct impact on the quality and efficiency of pellet production.
2. Types of pellet mill dies
Pellet mill dies are mainly divided into two types:
(1) Ring die
A ring die is a cylindrical die with multiple perforations on the outer layer. This type of die is usually used in conjunction with a ring die pellet machine and is suitable for large-scale industrial production. Ring dies have the following characteristics:
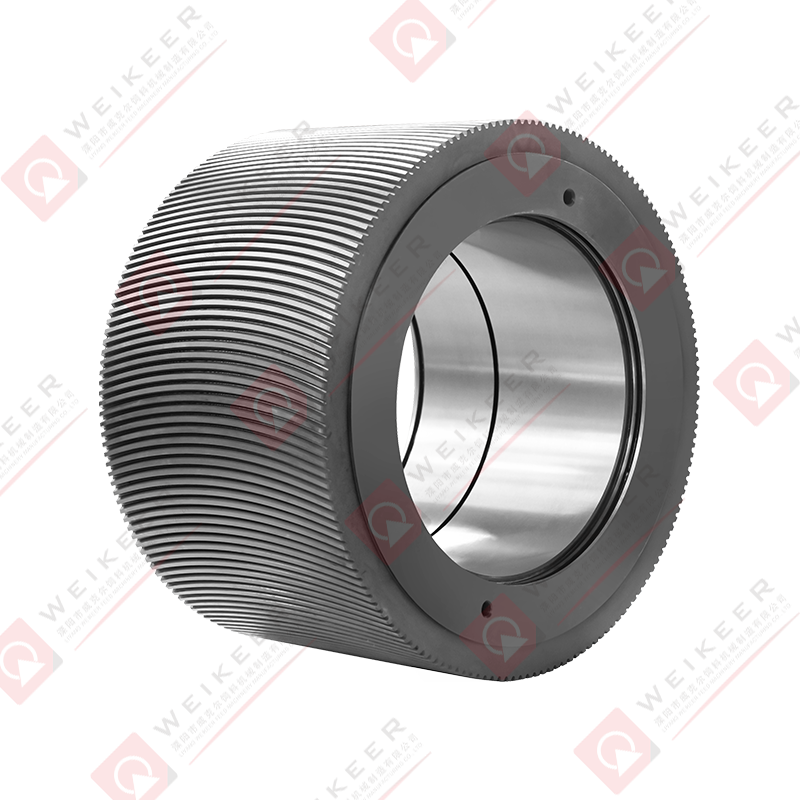
Suitable for large-volume production and high efficiency
Uniform pellet quality and high density
Suitable for feed processing, wood pellets, biomass fuel and other industries
(2) Flat Die
A flat die is a flat-shaped die suitable for flat die pellet machines and is commonly found in small and medium-sized pellet production equipment. Its characteristics include:
Suitable for small-scale production and simple structure
Low maintenance cost and easy replacement
Suitable for family farms, small feed mills or wood pellet production
3. Pellet machine die manufacturing materials
Pellet machine dies are usually made of high-strength wear-resistant alloy steel to ensure their stability under high pressure and high temperature environments. Common materials include:
(1) Stainless steel mold
Suitable for food-grade and pharmaceutical-grade pellet production
High corrosion resistance, suitable for materials with high humidity
(2) Alloy steel mold
Good wear resistance and impact resistance
Suitable for high-hardness materials such as feed and wood pellets
(3) Carbon steel mold
Low cost, suitable for short-term use
Suitable for small-scale production or industries with low wear resistance requirements
4. Key factors affecting pellet machine mold performance
The performance of pellet machine mold directly affects the quality and production efficiency of pellets. The following factors are crucial:
(1) Aperture size
The mold aperture determines the diameter of the pellets. Common pellet size ranges are as follows:
Feed pellets: 2mm, 4mm, 6mm, 8mm (suitable for poultry, pigs, cattle, fish, etc.)
Wood pellets: 6mm, 8mm, 10mm (suitable for biomass fuels)
Chemical pellets: special apertures, depending on production requirements
(2) Compression ratio
The compression ratio is the ratio of the mold aperture to the hole length, which determines the density and hardness of the pellets. For example:
High compression ratio: higher particle density, suitable for wood chips and biomass pellets
Low compression ratio: looser particles, suitable for animal feed
(3) Hole design
The shape of the mold hole affects the fluidity and molding effect of the raw material. Common hole shapes include:
Straight hole: suitable for ordinary feed and biomass pellets
Stepped hole: suitable for high-density pellets, increase production
Tapered hole: reduce material blockage and increase mold life
5. How to choose a suitable pellet machine mold?
When choosing a pellet machine mold, the following factors need to be considered comprehensively to ensure production efficiency and pellet quality.
(1) Choose according to raw materials
Different raw materials have different hardness and viscosity, and need to match the appropriate mold. For example:
Soft raw materials (such as corn and soybeans): low compression ratio molds can be selected
High hardness raw materials (such as wood chips and straw): high compression ratio molds are required to ensure the density of the pellets
(2) Select according to production needs
Small family farms or laboratories: flat die pellet machine molds are recommended, which are easy to operate and low cost
Large-scale production: ring die pellet machine molds are recommended, which are more efficient and suitable for long-term stable production
(3) Pay attention to the wear resistance of the mold
Choosing wear-resistant materials (such as stainless steel and alloy steel) can extend the service life of the mold, reduce replacement costs, and improve production stability.
(4) Production cost and benefit
Although the initial cost of high-quality molds is higher, their service life is long. In the long run, they can reduce maintenance and replacement costs and improve overall economic benefits.
6. Daily maintenance and care of pellet mill dies
In order to ensure the long-term stable operation of the dies, the following maintenance measures are recommended:
Regular cleaning: Use high-pressure air or professional cleaning tools to clean the die holes to prevent clogging
Lubrication and maintenance: Add lubricant in appropriate amounts before and after the die is used to reduce friction
Check the wear: Check the wear of the die holes regularly. If the aperture becomes larger or the surface is uneven, it should be replaced in time
Storage precautions: Store in a dry and ventilated environment to avoid moisture causing rust on the die
Pellet mill dies (Pellet Mill Dies) are the core components in the pellet production process and directly affect production efficiency, pellet quality and operating costs. Different types of dies are suitable for different production needs. Correct selection and maintenance of dies can significantly improve production efficiency. Whether in feed processing, biomass fuel manufacturing, or pharmaceutical and chemical fields, suitable pellet mill dies can ensure efficient and stable pellet production, thereby enhancing the market competitiveness of enterprises.