In feed processing and biomass pellet production, pellet feed machines play a vital role. The anchored stainless steel ring die is one of the core components of the pellet feed machine, which directly affects the quality of the pellets, production efficiency and long-term performance of the equipment.
Stainless steel ring dies have high corrosion resistance, wear resistance and high strength, and can work stably for a long time under high load and high temperature environments. In order to improve the service life of the ring die, modern pellet feed machines often use anchoring technology, so that the ring die can be more firmly fixed in the machine body to avoid vibration and displacement under high pressure.
Working principle of pellet feed machine ring die
The working principle of the pellet feed machine is based on the process of compression and molding of materials when passing through the ring die channel under high pressure. The specific process is as follows:
Material enters the pressing area:
The material in the pellet feed machine enters the ring die area through the feed inlet. The material usually includes grains, plant powders, animal by-products, etc., which are pretreated and mixed to form a uniform mixture suitable for pressing.
Material compression molding:
As the ring die and the roller rotate, the material is subjected to high pressure and begins to pass through the dense channels on the ring die. At this time, the material will be squeezed and gradually formed into a particle shape. The size and structure of the ring die channel determine the size and density of the particles.
Particle discharge:
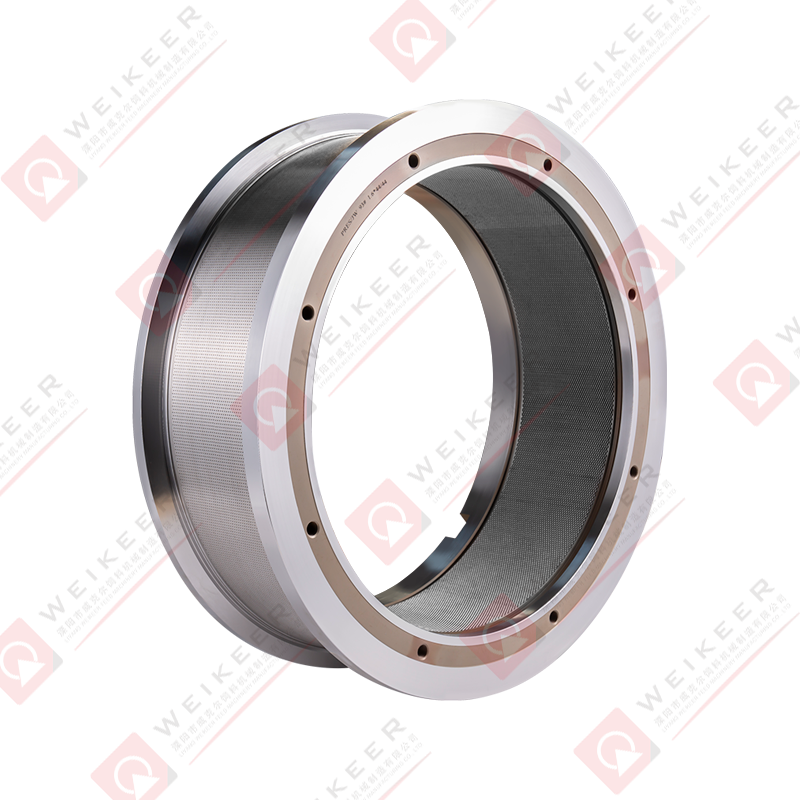
After the material passes through the channel of the ring die, the particles that have been pressed into a certain shape are discharged through the outlet of the ring die. The particles are cut into a specified length by a cutting device and eventually become finished particles for further processing or packaging.
Due to the high strength and corrosion resistance of stainless steel ring dies, they can maintain stable performance and improve production efficiency in high-pressure working environments.
Design and advantages of anchored stainless steel ring dies
Anchoring design:
The anchored stainless steel ring die uses special anchoring technology to ensure that the ring die is stably fixed in the pellet feed machine, avoiding displacement or vibration problems that may occur during high-speed operation. The anchoring design improves the working stability of the ring die and reduces the frequency of maintenance and replacement.
High temperature resistance and corrosion resistance:
The stainless steel material makes the ring die have excellent high temperature resistance and corrosion resistance, and can withstand the heat generated by the pellet feed machine during long-term operation and the acid and alkali substances in the material. This allows the ring die to maintain a long service life in harsh working environments.
Improve pellet quality:
The anchored stainless steel ring die can effectively control the density, hardness and smoothness of the pellets, thereby improving the quality of feed pellets. The uniformity of the pellets not only directly affects the digestion and absorption of the feed, but also affects the growth and health of the animal.
Energy saving and high efficiency:
Due to the optimization of the ring die structure and the application of anchoring technology, the overall operating efficiency of the pellet feed machine has been significantly improved. The material pressing process is more efficient and energy consumption is reduced, which helps to reduce production costs and improve corporate competitiveness.
Application areas of anchored stainless steel ring die
Feed production:
In the feed production process, anchored stainless steel ring dies are widely used in the pellet processing of various animal feeds, such as poultry feed, pig feed, cattle feed, etc. Its stability and efficiency can meet the needs of large-scale feed production.
Biomass pellet production:
Anchored stainless steel ring dies are not limited to feed processing, but are also widely used in the production of biomass pellets, such as wood chip pellets, straw pellets, etc. The production of biomass pellets requires high-strength and high-precision ring dies to ensure the high density and uniformity of the pellets.
Fertilizer and food industry:
In addition to feed and biomass pellets, anchored stainless steel ring dies are also used in fertilizer production and certain food processing processes, such as the production of starch pellets and sugar pellets. Its wide range of applications makes ring dies an indispensable production tool in many industries.
Future trends and challenges
With the advancement of science and technology, the design and technology of pellet feed machines are constantly innovating, and the technology of anchored stainless steel ring dies is also gradually developing. In the future, the materials of ring dies will be more diversified, and high wear resistance and long life will become the focus of research and development. At the same time, the introduction of energy-saving, environmental protection and automated control technology will also make the pellet production process more efficient and intelligent.
With the expansion of production scale, the requirements for the precision and quality of ring dies are getting higher and higher, which poses higher challenges to manufacturers. How to reduce the maintenance cost and replacement frequency of ring dies while ensuring production efficiency will be the key to the development of the industry.
The anchored stainless steel ring die for pellet feed machine plays an irreplaceable role in feed processing, biomass pellet production and other related fields. With its high strength, corrosion resistance and excellent working performance, the anchored stainless steel ring die effectively improves the efficiency and quality of pellet production. With the continuous advancement of technology, the future ring die will be more powerful and intelligent, bringing more efficient and energy-saving production solutions to related industries.