In modern feed, biomass energy and chemical industries, pellet mills are one of the indispensable equipment. It is widely used in animal feed production, wood chip fuel manufacturing and chemical raw material processing by compressing raw materials into uniform pellets. The performance and efficiency of pellet mills depend largely on its core components - press rollers and shells.
Basic functions of press rollers and shells
The working principle of pellet mills is to squeeze loose raw materials into dense pellets through the interaction between press rollers and shells. Press rollers are the key moving parts of pellet mills, usually made of high-strength alloy steel, and the surface is specially treated to enhance wear resistance and corrosion resistance. The shell is a fixed part, usually in an annular structure, with specific grooves or die holes designed inside for forming pellets.
During operation, the press rollers rotate around the shell, using strong pressure to squeeze the raw materials into the die holes of the shell to form pellets. Therefore, the quality of the press rollers and shells directly determines the production efficiency, pellet quality and service life of the pellet mill.
Main features of rollers and shells
High wear resistance
During operation, rollers and shells are subjected to great friction and pressure, so they must have excellent wear resistance. High carbon steel or alloy steel is usually used, and heat treatment, surface hardening or coating technology is used to improve wear resistance and extend service life.
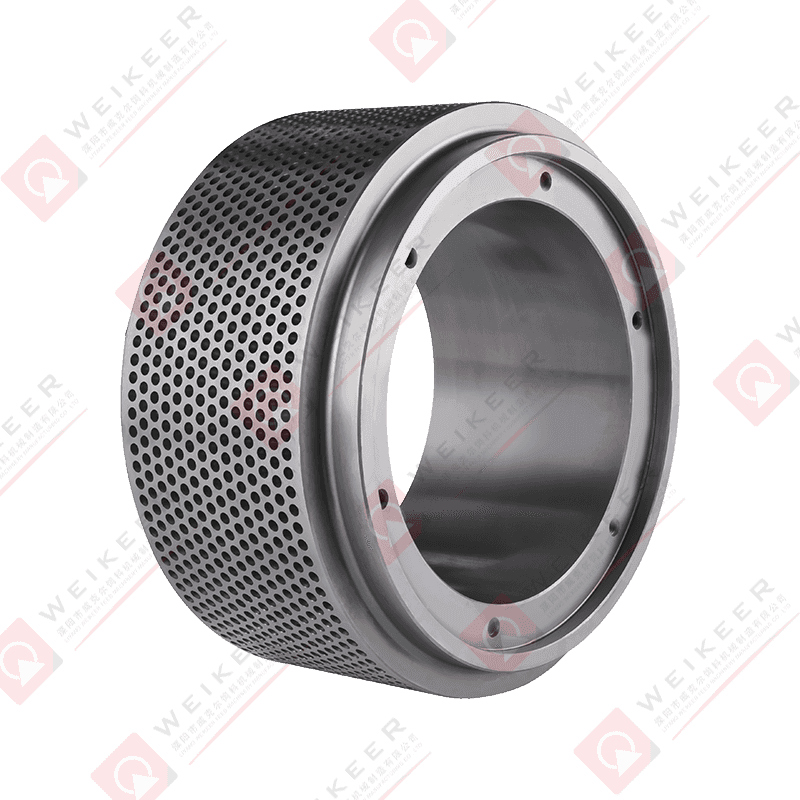
Precision machining
The surface accuracy and fit clearance of rollers and shells are crucial to the performance of pellet mills. Precision machining can ensure a close fit between rollers and shells, reduce energy loss and improve pelleting efficiency.
High temperature resistance and corrosion resistance
In some special applications, such as biomass pellet production or chemical raw material processing, the raw materials may contain corrosive components or require high temperature pressing. For this reason, rollers and shells are usually specially treated to adapt to harsh working environments.
Modular design
The rollers and shells of modern pellet mills are mostly modular in design, which is easy to replace and maintain. This design not only reduces maintenance costs, but also improves the overall flexibility of the equipment.
Diversity of application areas
The performance optimization of rollers and shells enables them to play an important role in many fields:
1. Feed production
In animal husbandry, pellet mills are widely used to produce animal feed. The efficient combination of the roller and the shell can compress raw materials such as grains and soybean meal into nutritionally balanced pellet feed for easy storage and transportation.
2. Biomass energy
With the development of renewable energy, biomass materials such as wood chips and straw are made into pellet fuel for power generation or heating. The durability of the roller and shell enables it to cope with these high-fiber raw materials and ensure the high quality of pellet fuel.
3. Chemical industry
In the chemical industry, pellet machines are used to make granular products such as catalysts and fertilizers. The corrosion resistance and high temperature resistance of the roller and shell enable it to adapt to the pelleting needs in complex chemical environments.
4. Environmental protection field
Pellet machines can also be used to treat waste, such as compressing sludge, plastic waste, etc. into pellets for further processing or recycling. The high-strength design of the roller and shell enables it to cope with these difficult tasks.
Technological innovation and development prospects
With the growth of market demand and the advancement of technology, the design and manufacturing of pellet mill rollers and shells are also constantly improving:
Application of new materials
The use of new alloy materials and composite materials will further improve the wear resistance and corrosion resistance of rollers and shells, while reducing weight and cost.
Intelligent monitoring
Combined with sensor technology and data analysis, future rollers and shells may be equipped with real-time monitoring systems to help users understand wear conditions and predict maintenance needs, thereby improving the operating efficiency of the equipment.
Environmental protection and energy saving
By optimizing the design of rollers and shells, reducing energy loss and waste of raw materials, pellet mills will be more in line with green environmental protection requirements.
As the core components of the equipment, the rollers and shells of pellet mills directly affect the efficiency and quality of pelleting. Their high wear resistance, precision processing and diversified applications make them an important part of modern industry. With the continuous development of technology, rollers and shells will demonstrate their value in more fields, providing more efficient and reliable solutions for feed, energy, chemical and other industries. In the future, this key component will continue to promote the advancement of pellet mill technology and help achieve global sustainable development goals.