The animal feed industry plays a vital role in ensuring the health and growth of livestock, poultry, and other farm animals. One of the most critical components of animal feed production is the pellet die, which is used to shape and compress raw feed ingredients into pellets. These pellets are easier to handle, store, and digest, offering various advantages in animal nutrition and feed efficiency. The design and quality of the pellet die significantly influence the overall performance of pellet mills and the final quality of the animal feed.
Material Quality: Pellet dies are made from high-quality, durable materials, usually stainless steel or alloy steel, to withstand the high pressures and abrasive nature of the feed ingredients. Stainless steel is preferred for its corrosion resistance, ensuring the die maintains its structural integrity over time, even when exposed to moisture, acids, and other harsh conditions.
Precision Engineering: The precision of the die holes is critical to producing high-quality pellets. The size and shape of the holes determine the pellet’s diameter, length, and density. High-precision dies ensure uniformity in pellet size, which improves the efficiency of animal feed and enhances the feeding process.
Durability and Longevity: Given the harsh operating conditions inside a pellet mill, including high temperatures and pressure, the durability of the pellet die is essential. High-quality pellet dies are designed to resist wear and tear caused by the constant friction with raw feed ingredients, ensuring a long service life and reducing maintenance costs.
Customization: Pellet dies can be customized to suit specific feed formulations and production needs. The number of holes, their size, and the spacing between them can be adjusted based on the type of feed being produced, the type of livestock, and the required pellet specifications.
Ease of Maintenance: Pellet dies are subjected to constant pressure and wear, so regular maintenance is necessary to ensure continued performance. Some advanced pellet dies feature designs that make it easier to clean and replace components, reducing downtime in the feed production process.
Enhanced Feed Efficiency: One of the main benefits of using pelletized feed is improved feed efficiency. Pelleted feed is more digestible and easier for animals to consume. Pellet dies allow for the consistent production of high-quality pellets, ensuring that animals receive the right nutrients in a form that is easy to digest. The uniform size and density of the pellets ensure that feed is consumed more efficiently, reducing waste and promoting healthier growth in animals.
Uniformity and Consistency: The uniformity of pellet size and shape is crucial for consistent feeding and optimal growth of animals. Animals tend to eat pellets that are of uniform size more readily, and consistent feeding patterns lead to more predictable growth and health outcomes. A well-designed pellet die ensures that the feed produced is of a consistent quality, which is essential for large-scale animal farming operations.
Storage and Handling: Pelleted feed is much easier to store and handle compared to loose feed ingredients. The compact nature of pellets makes them less prone to spoilage and contamination, and they are easier to transport and store. The pellet die plays a key role in creating pellets with the right texture and density, ensuring that the final product is durable and stable during storage.
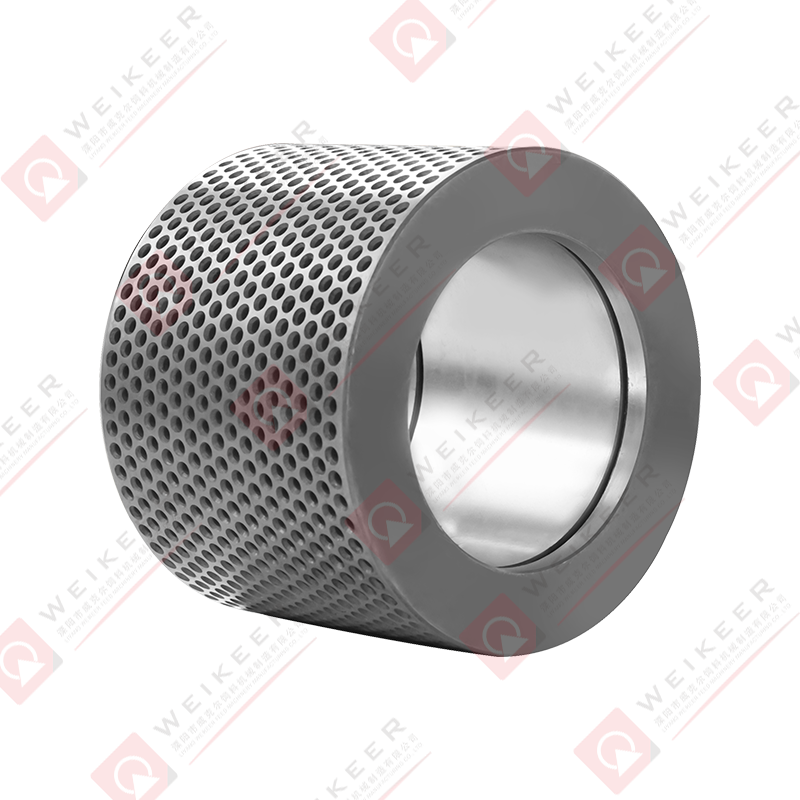
Improved Feed Conversion Ratio (FCR): The feed conversion ratio, which measures the efficiency with which animals convert feed into body mass, can be improved with high-quality pellets. By producing uniformly sized pellets with a precise formulation, pellet dies contribute to optimizing feed conversion, which is essential for cost-effective animal farming. Animals that consume well-made pellets are more likely to gain weight faster and more efficiently, leading to higher productivity in livestock operations.Flat Dies: Flat dies are the most common type of pellet die used in animal feed production. These dies feature a flat, circular surface with a series of holes, and they are typically used for producing smaller volumes of pellets. They are popular in smaller-scale operations and are known for their simplicity and ease of maintenance.
Ring Dies: Ring dies are typically used for large-scale commercial pellet production. Unlike flat dies, ring dies are shaped like a ring and have a continuous surface. The feed material is forced through the die ring, and the pellet mill’s rollers press the material against the die to form pellets. Ring dies are generally more durable and capable of producing higher volumes of pellets with uniform quality.
Factors to Consider When Choosing an Animal Feed Pellet Die
Feed Ingredients: The type of raw feed ingredients being processed will impact the choice of pellet die. Ingredients such as grains, grains with added fats, or high-protein animal feed require different die designs to achieve the desired pellet quality.
Pellet Size: The size of the pellets required for the animals will influence the die hole size and spacing. Smaller animals like poultry may require smaller pellets, while larger livestock such as cattle may require larger, denser pellets.
Production Volume: The scale of production plays a role in determining the appropriate pellet die. High-volume production facilities typically prefer ring dies due to their ability to handle large quantities of feed with consistent quality.
Maintenance Requirements: The ease of maintenance and the durability of the pellet die should be considered when choosing a die. A high-quality die with a long service life and minimal wear will save time and money in the long run.